WHAT IS MES?
The safest approach is to define a Manufacturing Execution System (MES) as Manufacturing Operations Management (MOM) that can be extended to include additional functionality to support the controlling, tracking, and documenting of the transformation of raw materials into finished goods in real-time.
5-minute read // ↓ Download PDF
What is MES: The Big Picture
Manufacturing companies must manage materials, shipments, money, people; and the like. These companies require systems to be in place from the upper end including finance, purchasing, sales, etc. all the way down to the plant floor where machine operators produce the correct product with the correct quality standards.
At the plant floor, these systems can be handled by computers and software, spreadsheets, notepads, verbal communications, or in the mind of a person who has learned through many years of experience. Whatever the system may be, it is in place and is working, otherwise, the manufacturer would go out of business due to missed shipments, poorly handled finances, poor product quality, etc.
At the upper end, systems exist commonly referred to as Enterprise Resource Planning (ERP), Manufacturing Resource Planning (MRP), or Advanced Planning System (APS). These systems handle receiving orders from customers, group into production orders, ensure there are enough raw materials on hand, schedule the equipment to run the production orders, etc.
At the lower end, there are systems in place to control the machinery. These systems consist of sensors, push buttons, special computers to control machines, Human Machine Interface (HMIs), etc. The operator can start, stop, and control other aspects of the machine operation. These systems alone do not have any knowledge of the product being produced, raw materials being consumed, etc. without the operator making manual entries nor are these systems required to run the machine.
2019: US manufacturing is the largest in the world. It produces 18.2% of the world's goods.
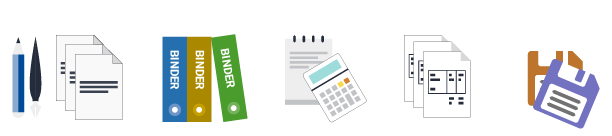
Typically, HMIs are local to a machine or process and don’t span across the entire facility. This is where Supervisory Control and Data Acquisition (SCADA) comes into play and commonly, but not always, is the same system as the HMIs. SCADA systems control processes locally or remotely, provide high-level monitoring, collect process data in real-time, maintain historical data, log events and alarms, etc.
Between the upper and lower end there is a layer that exists in every manufacturing company that is commonly referred to as MES. This is the system that is used to control, track, and document the transformation of raw materials into finished goods in real-time.
The primary functionality provided by an MES system includes:
- Detailed resource scheduling and status
- Dispatching production tasks and sequencing
- Traceability and genealogy
- Work-in-progress and inventory
- Ensuring quality
- Detailed maintenance management
- Work instructions and other document control
- Performance analyses
Some of these items are similar to what ERP or MRP systems provide but the level of detail needed at the plant floor is much greater than what is needed at the upper level. For example, ERP systems don’t need the details required to change over a machine to run a specific product or the steps to heat up a process prior to running a specific product.
MES is used to control, track, and document the transformation of raw materials into finished goods in real-time.
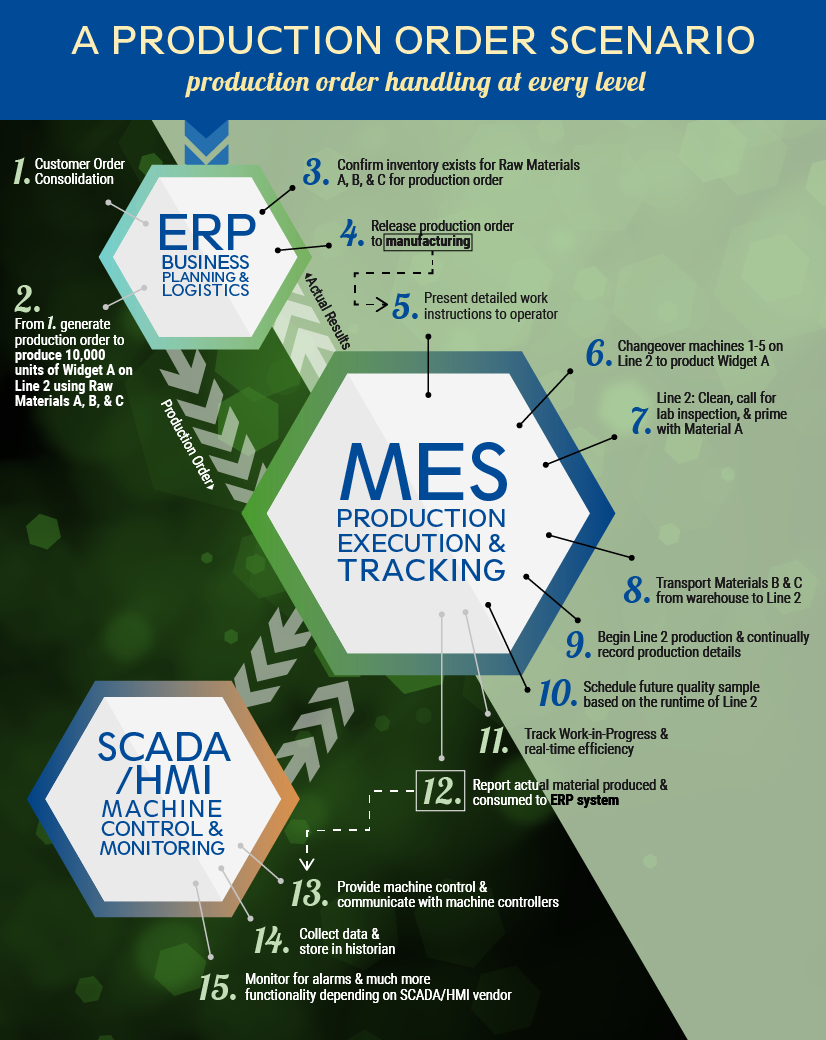
ERP systems are not real-time and are not designed to collect the amount of data at the rate that MES, SCADA, and HMI systems must. Typically, details about the finished goods, consumed raw materials, etc. are recorded by the ERP system when production is complete. The MES systems can track production by the second and, in some cases, less than a second. This means schedules, work-in-progress, performance indicators, quality, and more, are updated in real-time rather than at the close of business.
The image to the left represents a production order scenario. Notice the number of detailed steps required on the plant floor that the ERP system doesn’t need to manage.
ISA-95 Definition
The International Society of Automation (ISA) is an organization that sets standards for automation. One such standard is ISA-95, developed by a committee of volunteer industry experts. The ISA-95 Standard was created because the integration of business logistics systems with manufacturing systems is difficult and expensive. It provides a common nomenclature and model to describe controlling, tracking, and documenting the transformation of raw materials to finished goods.
ISA-95 uses the term Manufacturing Operations Management (MOM) to describe the space between the upper level and the lower level. Part of the ISA-95 standard specifically states content areas as: production operations management, maintenance operations management, quality operations management, and inventory operations management.
2018: US manufacturing accounted for $2.33 trillion of GDP.
Excited to learn more? Reach out to us to schedule a live demo today!
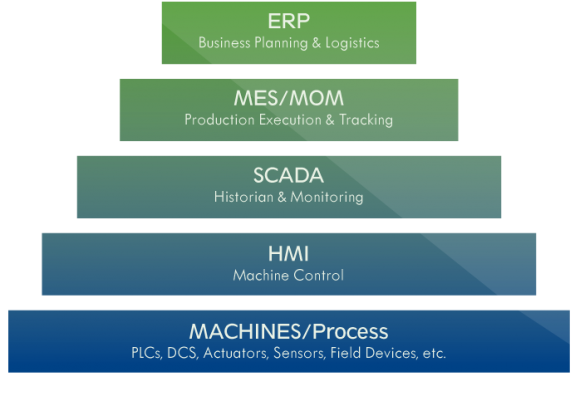
MES Defined
The term MES is used by broad audiences and contextually that makes it hard to agree upon a single definition. Depending on which source you reference, some state MES is a subset of MOM. However, the general use for the term MES actually includes more than what ISA defines within MOM.
More people tend to recognize the term MES instead of MOM since MES was established many years before ISA drafted the ISA-95 Standard and therefore, coined and defined the term MOM. Given this scenario, many vendors state MES in their product name or use it to describe their product because it is potentially more effective marketing-wise for them.
Some key MES research companies including Gartner, LNS, and ARC, include different types of functionality within their MES definitions. Some include functionality such as batch systems into MES while ISA excludes this from MOM.
Questions or Comments? Reach out to today!