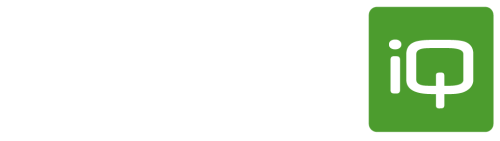
Revolutionizing Manufacturing Intelligence with AI-Powered SepaIQ
We’re in a race to innovate, armed with more Business Intelligence and Artificial Intelligence technology at our disposal than ever before. Yet, despite this and the vast amount of data available in modern manufacturing, most organizations struggle to turn it into actionable insights. According to Deloitte, “nearly 70% of manufacturers indicated that problems with data, including data quality, contextualization, and validation, are the most significant obstacles to AI implementation” [1]. As factories become more complex, data challenges can block progress, slow decisions, and reduce productivity. Addressing these challenges is no longer optional—it’s essential for staying competitive.
Key obstacles manufacturers face include:
- Outdated Technology Architecture: Many OT technologies on factory floors lag behind IT advancements, leading to inefficiencies and barriers between IT and OT. Current architectures often fail to support both high-level data analysis and efficient production operations.
- Complex Data Management: Systems like MES, ERP, and WMS frequently operate in isolation, using different connection methods and generating data in varied formats and contexts. This disconnect complicates data integration and requires time-consuming manual effort to consolidate information.
- Data Quality Issues: Clean, contextualized data is the foundation for advanced analytics and machine learning. Many manufacturers struggle with accuracy, requiring labor-intensive efforts to prepare and validate data before it can be relied on for upstream analysis or AI training.
- Lack of Real-Time Visibility: Providing a unified, real-time view of production is critical but difficult to achieve with disconnected systems. This limitation prevents the plant floor from taking immediate action.
How SepaIQ Transforms Manufacturing Analytics
Tackling these challenges requires a new approach—one that not only integrates disparate systems and contextualizes data in real time, but also ensures scalability and responsiveness to the needs of modern manufacturing. SepaIQ is designed to address these issues head-on, providing practical intelligence to empower both decision-makers and production teams.
High-Performance Analysis | Data Streaming and Reliability | Enhanced Connectivity | Contextualized Data | User-Defined Data Groups | Prediction Models for Machine Learning and AI | Real-Time Plant Floor Updates | Post-Production Updates
High-Performance Analysis
SepaIQ is built for speed and scalability without compromising critical production operations. By efficiently processing large datasets for real-time analysis, this tool provides a reliable foundation for advanced manufacturing intelligence.
- Clustered Analytics Servers: Production servers manage demanding tasks like batch mixing, packaging, and assembly, leaving limited compute capacity for data analysis. When these servers become overburdened, production slowdowns or interruptions can occur. By offloading analytics to independent servers, SepaIQ delivers ultra-high performance analytics while protecting the essential functions of HMI, SCADA, and MES.
- Load Balancing Compatibility: SepaIQ is cluster-based and supports load balancing to handle variable workloads, allowing multiple servers to perform real-time analytics based on current resource demand. Configuration is managed at the cluster level, eliminating the tedious task of configuring each server. Additionally, a detailed event log provides visibility of all server activity and errors within the cluster for streamlined monitoring and troubleshooting. This optimizes computing power, reduces costs, and minimizes the risk of interruptions caused by server overload.
- Efficient Data Storage and Modification Processing: SepaIQ’s lightweight database structure stores values only when they change, eliminating redundancy and reducing database size. Its flexible data storage system is especially valuable for managing time-series data and accommodating after-the-fact adjustments often required in real-world production scenarios.
- Data Streaming and Reliability: SepaIQ conserves system resources and prevents overloading servers by streaming data in smaller, manageable sets, and performing calculations in the process. This is particularly important for processing large analytics requests, such as historical data queries, which could otherwise overwhelm system resources and disrupt operations. Additionally, SepaIQ leverages store-and-forward technology to prevent data loss during network failures.
Enhanced Connectivity
Modern manufacturers require unified visibility of all production data, regardless of source—whether from unmanaged databases or systems like MES, ERP, and WMS. SepaIQ consolidates data from diverse sources into a consistent structure, breaking down silos and supporting protocols like Kafka, MQTT (versions 3 and 5), OPC-UA, and RESTful API. Additionally, SepaIQ enables Continuous Integration and Continuous Delivery (CI/CD) workflows, allowing configurations to be versioned and managed in Git or similar repositories. Configurations can be imported and exported using the same JSON format as the RESTful API, providing seamless integration and management.
The communication flexibility SepaIQ provides for receiving data is equally available for transmitting data to higher-level BI And AI systems using pub-sub technologies. SepaIQ supports connectivity with a variety of data sources and sinks, empowering users to select the most efficient connection method to suit their needs. This ensures smooth data exchange and real-time updates both into and out of the SepaIQ data hub.
Contextualized Data
Data from disparate systems often comes in varying formats and contexts, making it challenging to combine for system-wide metrics, ad-hoc reporting, or AI model training. Without a clear plan, loading terabytes of data into the cloud can result in an unusable “data swamp”. To enable analysis and identify trends, data from multiple sources must first be aligned and enriched with meaningful context. For instance, temperature data from a mixing tank sensor is only valuable when paired with details like the machine state, the product being made, and the acceptable temperature range for that product. Without this context, the data is incomplete and lacks the reliable foundation needed to train AI or machine learning systems to learn patterns and make accurate predictions.
This challenge is so significant that data scientists often spend over 80% of their time preparing data for AI training. Even then, by the time raw data reaches them, critical manufacturing context and domain knowledge may be lost or hard to recover. SepaIQ addresses this issue by equipping plant-floor staff—those with deep expertise in manufacturing systems and processes—to contextualize and prepare data at the source, providing accurate, context-rich information ready for advanced analysis.
User-Defined Data Groups
As explained above, uniform data contextualization across all sources is essential for higher-level analysis. SepaIQ allows the user to define this context, enabling them to customize data group hierarchies and analytics requests to align with their organization. For example, the ISA-95 standard prescribes a hierarchy that includes levels such as Enterprise, Site, Area, Line, Cell, Process Cell, and Unit. Some users, however, may require additional granularity, such as including Business Unit, Region, or Cell Group levels to better reflect their operational structure. Data groups can be configured for any purpose, including concrete items (e.g., physical equipment), abstract groupings (e.g., logical classifications), or virtual items (e.g., digital twins). Whether adopting ISA-95, a modified version of this standard, or entirely custom hierarchies, SepaIQ provides the flexibility to tailor data structures to each organization’s unique needs. This functionality not only supports compliance with manufacturing standards like ISA-95, but also aligns with the Unified Namespace (UNS) concept in Smart Manufacturing, facilitating data democratization and comprehensive, customizable data management.
Prediction Models for Machine Learning and AI
A factory is a dynamic network of moving parts, where countless things can go wrong on any given day. Traditional MES systems focus on reporting past events, helping manufacturers identify areas for improvement and refine processes over time—SepaIQ does this, and also takes it a step further by using machine learning to forecast potential future events before they happen. Prediction models are trained on real plant data, such as historical production schedules, operator shift performance, machine cycle times, raw material quality metrics, and even environmental variables, to uncover patterns and relationships between these factors and past losses and quality issues. By analyzing these patterns, SepaIQ can identify key contributors to problems and predict when similar issues might happen again based on current production conditions.
For example, SepaIQ can predict the production loss for the day and determine the probability for each likely loss reason. It might predict that a machine is at high risk of starvation due to inconsistent material delivery from an upstream station or detect a high probability of defects linked to variability in a newly sourced ingredient. Armed with this foresight, production and maintenance teams can proactively investigate and address potential issues before they disrupt operations.
In addition to prediction models, SepaIQ features Sentiment Analysis, which evaluates textual input, such as operator notes or comments, to analyze emotional tone and word choice. By identifying patterns in language and connecting them to actual production outcomes, SepaIQ creates a sentiment model tailored to each manufacturer’s specific goals and objectives. This model determines the sentiment of textual data and can classify emotions such as frustration, anger, or satisfaction. In a manufacturing setting, this technology might detect operator frustration with a specific machine or process that, if ignored, could escalate into equipment failure or bottlenecks. It could also uncover low morale, pinpoint training gaps, flag unclear instructions, or reveal other inefficiencies that impact performance.
Real-Time Plant Floor Updates
Analysis results, loss predictions, and defect forecasts are no longer confined to high-level reports—they’re instantly delivered directly to the shop floor, where they have the greatest immediate impact. Whether powered by SepaIQ’s analysis and machine learning models or generated by external AI or BI tools, these results flow back into Ignition for real-time display on dashboards, HMIs, and reports. This dynamic feedback loop fosters a culture of responsiveness, where data is no longer just a tool for retrospective analysis but a driving force for immediate action.
Post-Production Updates
In the real world of manufacturing, data doesn’t always arrive all at once, and post-run corrections are unavoidable. Downtime reasons may be revised or quality results may arrive after lab tests are complete. Managing these updates effectively is essential to maintain accurate data—and accurate data is the foundation of reliable predictions.
SepaIQ streamlines this process by saving values to the database only when they change. This approach makes it simple to modify or remove previously recorded entries or retroactively insert missing data. When updates occur, adjacent data within the same time period is automatically adjusted, and all subscribers—whether connected through a broker or directly—immediately receive the updated results.
Conclusion
SepaIQ is not just another analytics tool—it’s a paradigm shift in how manufacturers interact with their data. By providing actionable insights directly to the factory floor, bridging the gap between high-level analysis and daily operations, and simplifying advanced analytics, SepaIQ equips manufacturers with the means to address today’s challenges while preparing for the opportunities of tomorrow.
Whether it’s predicting production losses, uncovering quality issues, or empowering operators with real-time information, SepaIQ transforms data from a passive resource into a proactive force for change. This innovation promotes not only better decision-making but also a culture of responsiveness and continuous improvement, where every piece of data contributes to greater operational success
The future of manufacturing belongs to those who can seamlessly connect data, technology, and people. With SepaIQ, manufacturers gain a competitive edge by turning complexity into clarity and potential into performance.
Schedule a demo to see how SepaIQ can revolutionize your operations.
About Sepasoft®
Sepasoft® provides a modular approach to building Enterprise-Class MES solutions using OEE, Track & Trace, SPC, and Recipe & Changeover Modules. The result is a custom solution tailored for your manufacturing needs that integrates nicely with your ERP, Inventory Management, and Asset Management Systems. For more information, visit sepasoft.com.
Sources
1 – https://www2.deloitte.com/us/en/insights/industry/manufacturing/manufacturing-industry-outlook.html
Learn more about the SepaIQ here: https://www.sepasoft.com/products/sepaiq/.
Have Questions? Reach out to us: info@sepasoft.com