OEE Downtime
The Sepasoft® OEE Downtime Module offers many features to help you maximize manufacturing effectiveness.
Tracking overall equipment effectiveness (OEE) and downtime just got easier. The Sepasoft® OEE Downtime Module empowers manufacturers to reduce operating costs while increasing asset utilization and operating efficiency, resulting in improved profitability.
Some features include:
- Real-Time Efficiency Tracking
- Downtime Data Collection
- At-a-Glance Executive Dashboards
- Easy Enterprise Resource Planning (ERP) Integration
- Mobile MES Access
- Production Scheduling
- Fast, Customizable Implementation
- Automatic Data Collection
- And more!
OEE Enhanced Production Scheduling allows you to visualize the OEE production schedule including actual versus targeted production, machine status, delayed production, and more in real-time. Scheduled production entries can be obtained from a higher level enterprise resource planning (ERP) system, manually, or by simply dragging a work order onto the schedule.
Breaks and other routine workday events are displayed on the same schedule by providing a complete intuitive view of current and upcoming production activities. Schedule entries are automatically adjusted to accommodate production progress, breaks, and other factors that affect production in real-time.
Scheduled production is dispatched to equipment operators, warehouse staff, quality technicians, and more to keep everyone working with the up-to-the-minute production schedule.

The OEE Downtime Module accurately tracks production counts and other key data when running multiple products on a line. Our OEE Downtime Module also supports running changeovers with two or more products running on a production line simultaneously, in addition to supporting many other production scenarios.
Tracking a product’s progression through a line’s sub-equipment (cells) is effortless and can be triggered by the Equipment Operator or automatic signals sent from the equipment.
The OEE Downtime Module handles Equipment Statuses in two parts–logistical and local. Consider that the local status (Equipment State) indicates if the equipment is running or down with a fault. Meanwhile, the logistical status (Equipment Mode) indicates what the equipment is purposed for at some time: changeover, production, or maintenance.
By capturing the local and logistical status of equipment, we represent valuable context for production data. Both status levels can be configured with custom values for different equipment and organized in logical groupings so each piece of equipment has the correct asset utilization categories and downtime reasons.
The analysis capabilities open up new insights into equipment statuses. Consider the case of an estop pressed on a machine. This is valuable information during production, but expected and not valuable during maintenance activity. By filtering out maintenance status, the valuable data comes to the forefront and can be utilized for continuous improvement.
Downtime Detection Methods
A variety of OEE downtime detection algorithms accommodate different equipment layouts to provide the true cause of OEE downtime events. Primary production equipment commonly contains multiple sub-equipment items (cells), and based on the selected OEE downtime detection algorithm, the system will determine the root cause that the primary equipment is not in production.
Simple equipment state, initial reason, parallel cells, the key reason, and more OEE downtime detection algorithms can be used at the production line level or cell groups that support a wide variety of scenarios. The key reason algorithm supports the key cell being located anywhere within the line and considers backups or starved conditions to determine the root cause of the OEE downtime event.
When there are equipment layouts where the root cause is not appropriate, the OEE Downtime Module tracks cycle times that can be used to determine bottlenecks in product flow. Blocked or starved times are tracked separately to support narrowing in on actual equipment OEE downtime events.
Operators can visualize OEE downtime events as they occur in real-time. With the most common configuration, the begin and end times of each event are automatically recorded, completely eliminating inaccurate timed data. OEE downtime events can be overridden or split to ensure that more accurate and actionable results are provided. In addition to the OEE downtime event details, free-form text notes can be entered to increase the actionable data used for process improvement.
Interactions between sub-equipment (cells or groups of cells) on a line can be viewed with the OEE graphical timing chart to diagnose and optimize product flow.
OEE equipment modes, states, counts, shifts, standard rates, user-defined addition factors, and more are always monitored and recorded on change events. This supports real-time production tracking but also supports adding additional data after the fact or correcting past recorded values.
Built-in store and forward through Message Queuing Telemetry Transport (MQTT) fills in gaps in the recorded data in the event of network outages.
The OEE Downtime Module has a built-in analysis engine that reads the recorded data and calculates different values including OEE, cycle times, and production counts. OEE Impromptu Analysis enables the user to include data points for multiple date ranges allowing them to see results on the fly. Then they can group the data to narrow down inefficiencies. For example, they might start with OEE downtime by shift, then add an operator to diagnose if additional operator training is needed.
Use the result from OEE impromptu analysis to create dashboards and add-on displays to make production information visible.
OEE Impromptu Analysis allows you to keep analyses private, share with a group, or make public depending on the analysis security settings. A couple of options for analysis settings security include permission settings for user roles that determine who can modify and/or execute the analysis settings. A user who can modify helps keep unwanted modifications from happening, whereas a user who can execute allows analysis results visible to anyone contributing to efficiency improvement.
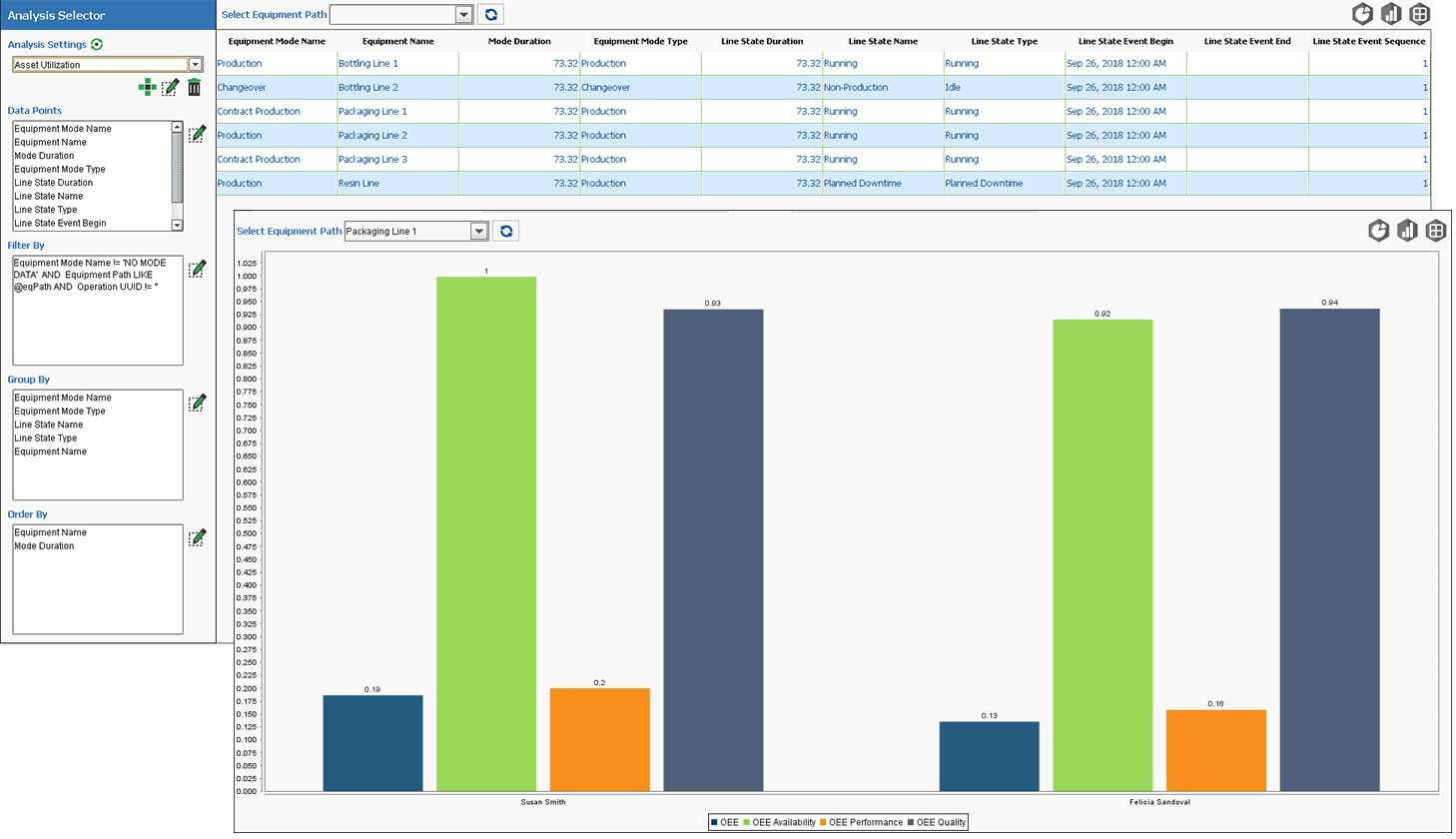
For common production metrics that reflect up-to-the-minute conditions, Live Analysis is used to automatically recalculate analysis as production events occur or can recalculate at a configurable interval, whichever comes first. Each line and its sub-equipment (cells) can have multiple Live Analyses active that can be based on the day, shift, run, or custom time period. The analysis engine uses a proprietary caching algorithm to return the results in real-time.
The Material Manager component allows you to easily define production settings and control the production line, cell groups, cells, etc. Make unique adjustments for each material and equipment combination down to the sub-equipment (cell) level. This enables your company to correctly set OEE production rates, select cells, and other settings to help your production run smoothly.
The OEE module is built in compliance with the ISA-95 standard, providing a consistent model and terminology for production control and tracking. The ISA-95 standard has been vetted by many manufacturers and applied to many processes and has been proven valuable over many years. ISA-95 compliant Sepasoft MES Modules include OEE Downtime, Track & Trace, and Settings & Changeover. Sepasoft® uses ISA-95 to provide seamless integration between lot tracking, production control, OEE, and downtime tracking solutions.
ISA-95 compliance allows you to utilize an open standard (as opposed to a vendor’s proprietary system) providing you the ability to share data with an ERP or other business systems.
OEE Modules Comparison Matrix
Quickly identify and focus your efforts on the top downtime reasons affecting your operating efficiency.
Feature | Benefit | Standard | Enterprise |
Downtime Analysis | Accurately determine the root cause for loss of production with advanced downtime detection algorithms. | ||
Easy Ad-Hoc Analysis | Pinpoint production inefficiencies with customizable ad-hoc analysis, allowing users to select unique combinations of data values, filters, groupings, and orders. | ||
Post-Run Corrections | Keep KPIs, analysis results, and historical data accurate with the ability to adjust previously collected production data. | ||
Chart & Table Drill Down | Achieve a deeper understanding of OEE analysis with chart and table drill-down functionality. | ||
Historical Analysis | Identify downtime trends and target areas for improvement by retaining and analyzing unlimited amounts of past production data. | ||
Record Custom Data Items | Evaluate how non-OEE factors (e.g. vendor, tooling) are affecting efficiency by incorporating custom data items into your analysis. | ||
Automated Production Reports | Reliably communicate OEE results across the organization by integrating with Ignition Reporting to automatically generate and send reports via email or other methods. | ||
Multiple Site Analysis and Reporting | Monitor production efficiency across all operations of your global enterprise by comparing OEE and production results across sites and production areas. |
Drive continuous improvement by responding to production issues in real-time.
Feature | Benefit | Standard | Enterprise |
Real-Time OEE Scores | Respond to production issues as they happen with live notifications and visual feedback showing overall OEE, availability, performance, and quality scores. | ||
Dynamic Dashboards | Share meaningful information using real-time custom dashboards tailored to the needs of your company. | ||
Real-Time Equipment Data Collection | Minimize error and reduce manual input by capturing equipment data automatically, freeing up operators to focus on their primary task of producing product. | ||
Equipment Timing Chart | Determine the root cause of downtime events and optimize material flow by visualizing interactions between line equipment. | ||
Live KPIs | Configure custom Key Performance Indicators (KPIs) that will best help your organization improve production efficiency. |
Easily adapt to organizational growth with a unified MES solution that supports change over time. Sepasoft MES expands from the edge-of-network up to a global enterprise with no rework or loss of data.
Feature | Benefit | Standard | Enterprise |
MES Server Health Monitoring | Detect and resolve system issues before they cause loss of production with out-of-the-box health monitoring tools. | ||
IIoT/MQTT Functionality | Prevent the loss of historical data, optimize network bandwidth, and improve security by capitalizing on IIoT, with built-in MQTT and OPC/UA support. | ||
Unlimited Lines per Site Licensing | Scale your MES system as your organization grows without significant licensing costs or hidden fees. Unlike alternatives, a Sepasoft site license includes unlimited lines and machines. Users, screens, reports, and field device connections are unlimited within a site license. | ||
Multiple Site Production Data Synchronization | Improve visibility and reliability throughout the enterprise by easily sharing schedules, production results, and more across multiple sites and servers. With out-of-the-box functionality, integration labor and custom coding are significantly reduced. | ||
Multiple Site Configuration Synchronization | Simplify the configuration process with automatic synchronization across multiple sites and servers. Minimize duplicate entry, misconfigurations, and other entry mistakes without custom coding. |
Customize system configuration to meet the unique requirements of your organization.
Feature | Benefit | Standard | Enterprise |
Automatic, Manual, or Hybrid Data Collection | Reduce operator workload with automatic data collection, with the option to collect valuable details manually. With the flexibility to collect data automatically, manually, or through a hybrid process, all relevant OEE information is captured. | ||
Data Export/Import Capability | Enjoy the freedom to use production data however you choose. Optionally, export and import data with external systems for further analysis or configuration. | ||
Material Management | Keep your key performance indicators (KPIs) accurate by configuring unique rates and settings for each material-equipment combination. | ||
Manage Documents & Artifacts | Ensure the correct versions of materials safety data sheets (MSDS), work instructions, travelers, and more are available when needed. Attach additional data files (e.g. images, PDFs, etc.) to schedules, work orders, materials, equipment, and more. | ||
Configurable Equipment Modes | Track asset utilization by configuring user-defined equipment modes that are most meaningful to your manufacturing process. User-definable modes can be anything but typically include changeover, set up, R&D, production, maintenance, and idle. | ||
Equipment Manager Component | Easily configure your equipment hierarchy in an intuitive representation of your plant floor. Define state, mode, and other settings unique by site, area, line, machine, and more. | ||
Detailed Changelog | Automatically record all changes made to any MES configuration to help you meet the challenges of regulatory compliance. Quickly zero in on significant changes with access to a complete audit trail of the location, date, type of change, responsible person, and more. | ||
Multi-Database Vendor Support | Simplify implementation by selecting the database vendor that best fits into your existing IT standards. |
Achieve production goals by tracking progress and monitoring production conditions using live visual feedback.
Feature | Benefit | Standard | Enterprise |
Running Changeover | Accurately track production counts and other key data when running multiple products on a line. Leverage built-in OEE algorithms that support running changeovers with two or more products running on a line simultaneously. | ||
Flexible Shift Configuration | Accurately predict production outcomes that match your shift schedules with flexible shift configuration, including rotating shifts and holidays. | ||
Live Plant Floor Scheduling | Determine whether you’re on track to meet production targets at any given moment. Plant floor scheduling is automatically updated and forecasted based on live production conditions, providing you constant feedback on the status of operations. | ||
Scheduling Analysis | Analyze past production runs to identify trends and carry forward successful practices to future operations and scheduling. | ||
Work Order Management | Fulfill production targets by tracking the real-time status of work orders, including units scheduled, produced, and remaining. Work orders spanning multiple runs or lines can be viewed in aggregate, providing the ability to review the work order as a whole. |
Transition from isolated systems and data silos to a coordinated, full-featured MES. With Sepasoft’s modular design, business systems of different functional areas can work together in harmony for greater insight.
Feature | Benefit | Standard | Enterprise |
Automatic Machine Settings Management | Manage machine settings to prevent quality issues and downtime. Identify deviations as they happen and quickly resolve critical issues with role-based management. To learn more, visit our Machine Settings Management (formerly Recipe & Changeover) product page. | ||
Document Management | Securely and easily manage production-related documents that are critical to safety, quality, and overall production efficiency. Build and distribute documents that operators can fill out and save with MES data for the historical record. To learn more, visit our Document Management product page. | ||
Synchronization to ERP Systems | Connect to your ERP or higher-level business system without custom development or the burden of maintaining high volumes of the script over time. Complicated scripts are replaced by a user-friendly visual interface to sequence communication and map data between systems. To learn more about ERP synchronization, visit our Interface for SAP ERP product page. To learn more about business systems connectivity, visit our Sepasoft Business Connector product page. | ||
Integrated Quality Tracking | Minimize waste and rework by catching quality issues early in the production process. Identify out-of-control variations with automatic alerts to resolve them before they become bigger (and more costly) problems. To learn more, visit our SPC product page. | ||
Integrated Traceability | Rapidly recall material genealogy from raw materials to finished goods, including real-time WIP inventory on the plant floor. To learn more, visit our Track & Trace product page. | ||
Compatible with Ignition | Save hours of customization by managing MES, SCADA, HMI, and more on a single platform with a unified operator interface and design tools. To learn more about the Ignition Platform, visit Inductive Automation’s Ignition Platform product page. |
To learn more or to purchase the OEE Downtime Module, contact Sales at 800-207-5506, select Option 1, or visit our pricing page.