Batch Procedure
Batch Procedure adds batch processing, continuous processing, and general procedure control, based on the ISA-88 Standard, to the Ignition® Platform.
Introduction to Batch Procedure
The Batch Procedure Module adds batch processing, continuous processing, and general procedure control, based on the ISA-88 Standard, to the Ignition® Platform. Recipe management is simplified by combining sequence control with parameter values in an intuitive graphical user interface. Real-time data collection of batch details provide analysis and electronic batch records.
Some features of the Batch Procedure Module include:
- Graphical Recipe Editor
- Separation of Recipes and Equipment Control
- Golden Batch Comparison
- Real-Time Batch Status Visibility
- Electronic Batch Records
- And much more
This module provides production staff with the tools needed to produce quality batches efficiently and consistently. With real-time monitoring tools and live visual feedback, quality issues can be identified before it’s too late.
Batch Formulas
Flexibly manage variations of your Batch Recipes by adjusting materials and settings without modifying core process logic. Whether making simple changes like color adjustments or fine-tuning ingredient ratios, you can quickly implement updates and save them for future use.
Excited to learn more? Reach out to us to schedule a live demo today!
Best-In-Class HMI
Sepasoft’s Batch Procedure Module is one of the few solutions that includes a natively integrated HMI. Unlike alternatives, there is no need to purchase an HMI solution separately or tediously map tags in a custom API.
Multiple Transfer Methods
Choose from multiple material transfer methods to best reflect existing equipment in the field. With the ability to run different recipes on each unit, the Batch Procedure Module easily adapts to your organization’s existing processes.
Pinpoint the source of quality issues and inconsistency with customizable ah-hoc analysis, allowing users to select unique combinations of data values, filters, groupings, and orders. Analyze unlimited amounts of past production data to identify trends and carry forward successful practices to future operations and scheduling.
Reusable Templates
Unit procedures or operations can be templated and reused for faster and easier development of recipes. Using this functionality, less time is spent on avoidable and repetitive configuration tasks.
Multiple Site Production Data Sync
Improve visibility and reliability throughout the enterprise by easily sharing schedules, production results, and more across multiple sites and servers. With out-of-the-box functionality, integration labor and custom coding are significantly reduced.
Securely and easily manage production-related documents to make complex manual processes more repeatable and consistent. Build and distribute documents that operators can fill out and save with batch data for historical record. Learn more about Sepasoft’s Document Management Module.
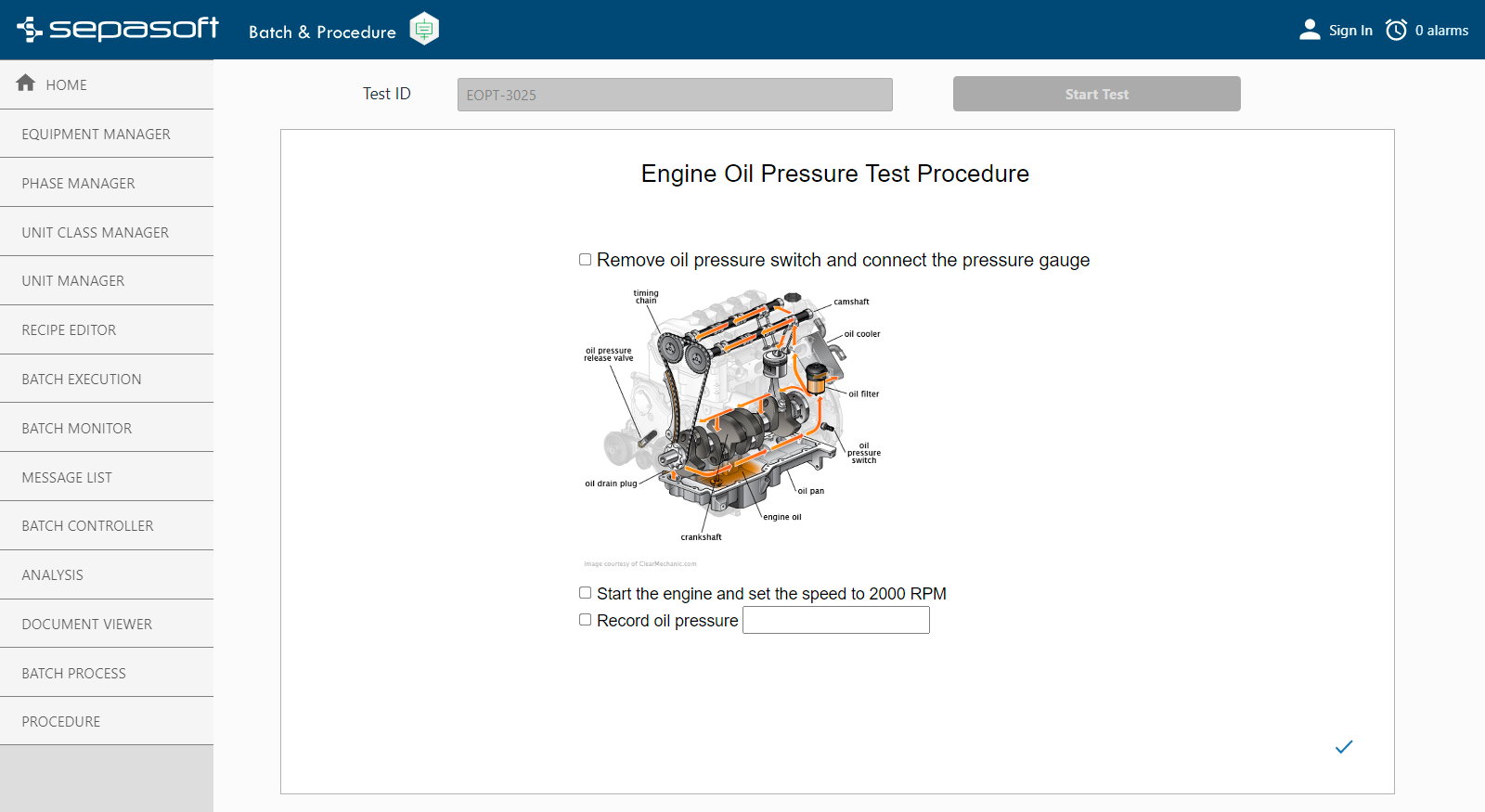
IIoT/MQTT Functionality
Prevent loss of historical data, optimize network bandwidth, and improve security by capitalizing on IIoT, with built-in MQTT and OPC/UA support.
Custom Parameter Calculations
Factor your organization’s custom requirements into batch parameters with dynamic calculations. Calculate ingredient quantities based on concentration, determine mix time based on humidity or temperature, and much more.
Simplified Validation Process
Simplify compliance validation using built-in tools such as versioning and a detailed changelog to target specific validation areas rather than revalidating the total process. All changes made to batch configuration are automatically recorded in a complete audit trail evidencing the location, date, type of change, responsible person, and more.
SCADA/HMI Integration
Save hours of customization by managing MES, SCADA, HMI, and more, on a single platform with a unified operator interface and design tools.
Batch Procedure Feature List
Designed with the user in mind, the Batch Procedure Module is modern, intuitive, and user-friendly. Minimize tedious configuration, thereby reducing development labor and allowing each individual to focus on their primary tasks.
Feature | Benefit |
Electronic Signatures | Promote accountability and compliance within your manufacturing process by evidencing approvals with electronic signatures. Incorporate any number of e-signatures from various roles into your batch recipe to ensure that approvals are properly documented for historical record. |
Graphical Recipe Editor | Simply edit recipes on one user-friendly screen using modern drag-and-drop technology. With less system training and and development labor required, Recipe Authors and Operations staff can more easily focus on the product. |
Separation of Recipes & Equipment Control | Empower Recipe Authors and Control Systems Engineers to specialize in their independent roles. With the separation of Recipes and Equipment Control, the cost of engineering and training is lowered throughout the life cycle of the manufacturing process. |
Reusable Templates | Unit procedures or operations can be templated and reused for faster and easier development of recipes. Using this functionality, less time is spent on avoidable and repetitive configuration tasks. |
Built-in Phases | Reduce development labor for each new recipe by utilizing standardized phases for frequently used tasks, such as displaying user messages, inventory checks, inventory updates, and more. |
Rapid Tag Mapping to Field Devices | Expedite the tag configuration process and minimize manual error with the ability to automate mapping to field devices. Any change to phase parameters results in automatic updates to all units referencing that phase. |
Local Processing Capability | Speed up the implementation process with the capability to execute phases locally on the batch server. Phases such as operator instructions and timers can be configured locally on the batch server without unnecessary and tedious mapping to PLCs. |
Graphical Unit Configuration | Intuitively arrange units in a graphical representation of the plant floor. Easily drag-and-drop to show unit connections and material transfer workflows. |
Achieve production goals by tracking progress and monitoring production conditions using live visual feedback. Standardize product results and minimize waste by ensuring the correct materials, equipment, and personnel are utilized at each step in the production process.
Feature | Benefit |
Batch & Procedure Use Cases | Control ISA-88 batch processes, manufacturing procedure-driven workflows, and hybrid processes in one toolset. Simplify maintenance and lower the total cost of ownership with a unified solution that easily fits into different types of protocols and workflows. |
Built-in UDT Interface | Streamline configuration and minimize error with access to a built-in UDT interface. Map a UDT to field equipment once, and every instance of this UDT will be automatically configured going forward. |
Run Recipes Simultaneously | Maximize equipment utilization by running multiple recipes simultaneously. Units can be intelligently allocated automatically, manually assigned, or a hybrid combination of the two. |
User Prompts/Message Handling | Create a more consistent, repeatable process by prompting operators with messages and instructions to guide equipment interactions. |
Document Management | Securely and easily manage production-related documents to make complex manual processes more repeatable and consistent. Build and distribute documents that operators can fill out and save with batch data for historical record. |
Live Plant Floor Scheduling | Determine whether you’re on track to meet production targets in any given moment. Plant floor scheduling is automatically updated and forecasted based on live production conditions, providing you constant feedback on the status of operations. |
WIP Inventory | Fulfill production targets by tracking real-time inventory based on customizable criteria such as material type, equipment type, material status, and more. |
Drive continuous improvement and product consistency by responding to production issues in real-time. Preserve the quality of each batch by identifying and resolving issues before it’s too late.
Feature | Benefit |
Best-in-Class HMI | Sepasoft’s Batch & Procedure Module is one of the few solutions that includes a natively integrated HMI. Unlike alternatives, there is no need to purchase an HMI solution separately or tediously map tags in a custom API. |
Real-Time Batch Status | Enable operators to easily check the status of a batch without an SFC (PFC) chart. With less navigation and drill-down required to monitor a batch, operators can focus on production. |
Dynamic Dashboards | Share meaningful information using real-time custom dashboards tailored to the needs of your company. |
Live KPIs | Configure custom Key Performance Indicators (KPIs) that will best help your organization improve production efficiency and quality. |
Real-Time Equipment Data Collection | Minimize error and reduce manual input by capturing equipment data automatically, freeing up operators to focus on their primary task of producing product. |
Easily adapt to organizational growth with a unified MES solution that supports change over time. Sepasoft MES expands from the edge-of-network up to a global enterprise with no rework or loss of data.
Feature | Benefit |
No-Nonsense Licensing | As your organization grows, scale your batch system without having to purchase more capacity. Users, screens, reports, and field device connections are unlimited within a site license! |
Unlimited Units per Site License | Roll out a batch implementation across your entire site without significant licensing costs or hidden fees. Unlike alternatives, a Sepasoft site license includes unlimited units. |
Multiple Site Production Data Synchronization | Improve visibility and reliability throughout the enterprise by easily sharing schedules, production results, and more across multiple sites and servers. With out-of-the-box functionality, integration labor and custom coding are significantly reduced. |
Multiple Site Configuration Synchronization | Simplify the configuration process with automatic synchronization across multiple sites and servers. Minimize duplicate entry, misconfigurations, and other entry mistakes without custom coding. |
Redundancy | Prevent disruption of mission-critical batch operations with a reliable solution enabling redundancy. In the event a server experiences technical failure, a second redundant server seamlessly takes over and continues executing automatically. |
Rapid Disaster Recovery | All batch configuration data is synchronized with other servers in your MES architecture, providing an up-to-the-minute production data backup. Any server within your MES architecture can be rapidly restored to production state without incurring any loss of data. |
IIoT/MQTT Functionality | Prevent loss of historical data, optimize network bandwith, and improve security by capitalizing on IIoT, with built-in MQTT and OPC/UA support. |
MES Server Health Monitoring | Detect and resolve system issues before they cause loss of production with out-of-the-box health monitoring tools. |
Optimize your batch process by analyzing large quantities of high-quality data to determine which factors produce the most success.
Feature | Benefit |
Golden Batch Comparison | Target the optimal recipe (“Golden Batch”) by examining which factors resulted in the most successful outcome. With access to large amounts of high-quality data, both effective processes and problematic events can be traced back to specific batches. |
Electronic Batch Records | Ensure that critical procedures are followed and automatically documented to evidence the results of each process step. These details are saved into electronic batch records and easily viewed alongside quality and traceability data documents. |
Easy Ad-hoc Analysis | Pinpoint the source of quality issues and inconsistency with customizable ah-hoc analysis, allowing users to select unique combinations of data values, filters, groupings, and orders. Analyze unlimited amounts of past production data to identify trends and carry forward successful practices to future operations and scheduling. |
Historical Analysis | Identify trends and target areas for improvement by retaining and analyzing unlimited amounts of past production data. |
Scheduling Analysis | Analyze past production runs to identify trends and carry forward successful practices to future operations and scheduling. |
Automated Production Reports | Reliably communicate results across the organization by integrating with Ignition Reporting to automatically generate and send PDF reports via email or other methods. |
Multiple Site Analysis and Reporting | Monitor consistency across all operations of your global enterprise by comparing quality results across sites and production areas. |
Customize system configuration and batch processes to meet the unique requirements of your organization.
Feature | Benefit |
User-Defined Batch Parameters | Create custom parameters to properly reflect your organization’s batch process. Define the tag type, custom calculations, data types, minimum/maximum values, and more. |
Multiple Transfer Methods | Choose from multiple material transfer methods to best reflect existing equipment in the field. With the ability to run different recipes on each unit, the Batch & Procedure Module easily adapts to your organization’s existing processes. |
Custom Parameter Calculations | Factor your organization’s custom requirements into batch parameters with dynamic calculations. Calculate ingredient quantities based on concentration, determine mix time based on humidity or temperature, and much more. |
Batch Formulas | Flexibly manage Batch Recipe variations, enabling material and settings adjustments without altering core process logic. Simple modifications like color change can be effortlessly implemented and saved for future use. |
User-Defined Script | Incorporate user-defined script into any recipe for customization beyond out-of-the-box functionality, such as queries to external systems, complex calculations, database queries, and more. |
Simplified Validation Process | Simplify compliance validation using built-in tools such as versioning and a detailed changelog to target specific validation areas rather than revalidating the total process. All changes made to batch configuration are automatically recorded in a complete audit trail evidencing the location, date, type of change, responsible person, and more. |
Automatic, Manual, or Hybrid Data Collection | Reduce operator workload with automatic data collection, with the option to collect valuable details manually. With the flexibility to collect data automatically, manually, or through a hybrid process, all relevant information is captured. |
Data Export/Import Capability | Enjoy the freedom to use production data however you choose. Optionally, export and import data with external systems for further analysis or configuration. |
Multi-Database Vendor Support | Simplify implementation by selecting the database vendor that best fits into your existing IT standards. |
Artifact Management | Ensure the correct versions of materials safety data sheets (MSDS), work instructions, travelers, and more are available when needed. Attach additional data files (e.g. images, PDFs, etc.) to schedules, work orders, materials, equipment, and more. |
Support for Multiple Testing Environments | Prevent undesirable results by testing and validating your batch system before going live. With our built-in features, push and pull changes between development, QA, and productions environments with ease. |
Transition from isolated systems and data silos to a coordinated, full-featured MES. With Sepasoft’s modular design, business systems of different functional areas can work together in harmony for greater insight.
Feature | Benefit |
SCADA/HMI Integration | Save hours of customization by managing MES, SCADA, HMI, and more on a single platform with a unified operator interface and design tools. |
Synchronization to ERP Systems | Connect to your ERP or higher level business system without custom development or the burden of maintaining high volumes of script over time. Complicated scripts are replaced by a user-friendly visual interface to sequence communication and map data between systems. |
Automatic Machine Settings Management | Manage machine settings to prevent quality issues and downtime. Identify deviations as they happen and quickly resolve critical issues with role-based management. |
Integrated Quality Tracking | Minimize waste and rework by catching quality issues early in the production process. Identify out-of-control variations with automatic alerts to resolve them before they become bigger (and more costly) problems. |
Integrated Traceability | Rapidly recall material Genealogy from raw materials to finished goods, including real-time WIP inventory on the plant floor. |
Material Management | Keep your key performance indicators (KPIs) accurate by configuring unique rates and settings for each material-equipment combination. |
To learn more or to purchase the Batch Procedure Module, contact Sales at 800-207-5506, select Option 1, or visit our pricing page