Multi-Dimensional Integration (MDI)
Sepasoft MES Premier Integrator
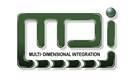
We are a systems integrator with experience in a wide array of industries and applications including critical infrastructure such as water/wastewater and power systems as well as manufacturing, pharmaceuticals, process control and food/beverage. We offer custom design solutions for new control systems, perform upgrades to obsolete control systems and provide onsite support services for all control systems. We also offer in-house panel assembly, and onsite installation. MDI has over 130 years of combined experience with all common controls platforms and would be happy to help you decide which platform fits your needs for your next project.
MES Certifications
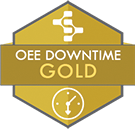
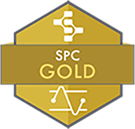
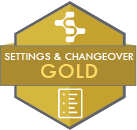
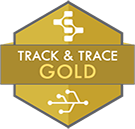
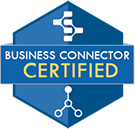
5 Gold, 1 Certified, AND 4 Credentialed MES ENGINEERS
2 LOCATIONS
Projects
Recipe Management for Access Equipment Mfr
McConnellsburg, PA
A leading manufacturer of access equipment had the need to improve a process in which
A leading manufacturer of access equipment had the need to improve a process in which machine frames are filled with shot manually. Previously when a frame was to be filled with shot, the frame would be weighed in station and be recorded on paper. The operator would then manually open a valve that would release shot to fill the frame, using their judgement to determine how much shot to be filled. The frame would then be weighed again and recorded. Using a handheld calculator, the operators would calculate the amount of shot filled.
MDI worked with the customer to create shot fill recipes for each model that the customer produces. When a frame enters, an operator will scan a barcode on the frame that Ignition uses to determine the model number. The model number is then used to load the specified recipe values to a PLC that controls the amount of shot fill sequence, ensuring that the frame has the correct amount of shot filled. When a frame is completed, the information is logged by model number, serial number, weight values, and date. The data was used to create reports that can be viewed by serial number, shift, and date.
The result of the project was a greatly improved process decreasing operator dependency and increasing overall quality. With a greater accuracy on the amount of shot filled, the amount of material wasted was vastly decreased. By having Ignition automatically log the shot fill information, operators were able to fill frames faster, eliminate paper logs, and have a quality record that can be accessed from anywhere on the customer’s network.
Since implementing this project, MDI has upgraded from MES version 1.0 to MES version 3.0 and converted the Vision application to Perspective.
MDI worked with the customer to create shot fill recipes for each model that the customer produces. When a frame enters, an operator will scan a barcode on the frame that Ignition uses to determine the model number. The model number is then used to load the specified recipe values to a PLC that controls the amount of shot fill sequence, ensuring that the frame has the correct amount of shot filled. When a frame is completed, the information is logged by model number, serial number, weight values, and date. The data was used to create reports that can be viewed by serial number, shift, and date.
The result of the project was a greatly improved process decreasing operator dependency and increasing overall quality. With a greater accuracy on the amount of shot filled, the amount of material wasted was vastly decreased. By having Ignition automatically log the shot fill information, operators were able to fill frames faster, eliminate paper logs, and have a quality record that can be accessed from anywhere on the customer’s network.
Since implementing this project, MDI has upgraded from MES version 1.0 to MES version 3.0 and converted the Vision application to Perspective.
RFID Tags and Scanners coupled with T&T
Pennsylvania
MDI collaborated with a heavy equipment manufacturer to integrate RFID tags and scanners coupled with
MDI collaborated with a heavy equipment manufacturer to integrate RFID tags and scanners coupled with the powerful Track and Trace module to track in-process frames being manufactured. This solution digitized the customer’s run schedule and provided real visualization of in process material.
RFID scanners were strategically placed to capture when frames would move in and out of all areas. Upon beginning the manufacturing process, operators mount an RFID tag inside the frame. Part information is automatically updated based on the new digitized run schedule. As the frame moved throughout the facility, the RFID scanners would recognize the tag and update its location via Track and Trace functions. Dashboards were placed throughout the facility so team members can see which parts are currently in robotic welders, getting filled with shot, being finished in paint, or completed in final assembly.
This project significantly reduced the amount of labor hours previously used by supervisors to locate parts throughout the facility. Before this project, each area had its own clipboard where team members would write down the current status. Track and Trace eliminated the need for paper record keeping riddled with human error and provided real time visibility in frame manufacturing.
RFID scanners were strategically placed to capture when frames would move in and out of all areas. Upon beginning the manufacturing process, operators mount an RFID tag inside the frame. Part information is automatically updated based on the new digitized run schedule. As the frame moved throughout the facility, the RFID scanners would recognize the tag and update its location via Track and Trace functions. Dashboards were placed throughout the facility so team members can see which parts are currently in robotic welders, getting filled with shot, being finished in paint, or completed in final assembly.
This project significantly reduced the amount of labor hours previously used by supervisors to locate parts throughout the facility. Before this project, each area had its own clipboard where team members would write down the current status. Track and Trace eliminated the need for paper record keeping riddled with human error and provided real time visibility in frame manufacturing.
2018-03-01 - 2018-07-01
Eliminating Paper Logs & Improving QA w/ SPC
Pennsylvania
A customer approached MDI with the need to improve their quality assurance process by decreasing
A customer approached MDI with the need to improve their quality assurance process by decreasing the number of manual measurements taken and eliminating paper logs. To do so, worked with the customer to implement Sepasoft’s SPC module across a paint line.
Some examples of the measurement values recorded and monitored include water temperature, oven temperature, pH, conductivity. Using the SPC module, MDI created an SPC system that continuously measures and records the different process values. MDI also developed mobile applications to replace hand-written paper documents. By continuously monitoring the various process values, any values that are outside of the spec/control limits triggers an HMI alarm that will instruct the operator on what to inspect, as well as what the corrective action is to take. Historical data is then used to create user-friendly reports to display SPC data.
By implementing the SPC project, the customer was able to eliminate paper logs and many manual measurements, saving them time and improving accuracy. The HMI alarms also decreased time in which the corrective action was able to be determined and improved quality by not allowing the line to run when values were beyond the spec/control limits. By visualizing historical data, the customer was able to view data trends to improve their manufacturing process.
Since implementing this project, MDI has upgraded from MES version 1.0 to MES version 3.0 and converted the Vision application to Perspective.
Some examples of the measurement values recorded and monitored include water temperature, oven temperature, pH, conductivity. Using the SPC module, MDI created an SPC system that continuously measures and records the different process values. MDI also developed mobile applications to replace hand-written paper documents. By continuously monitoring the various process values, any values that are outside of the spec/control limits triggers an HMI alarm that will instruct the operator on what to inspect, as well as what the corrective action is to take. Historical data is then used to create user-friendly reports to display SPC data.
By implementing the SPC project, the customer was able to eliminate paper logs and many manual measurements, saving them time and improving accuracy. The HMI alarms also decreased time in which the corrective action was able to be determined and improved quality by not allowing the line to run when values were beyond the spec/control limits. By visualizing historical data, the customer was able to view data trends to improve their manufacturing process.
Since implementing this project, MDI has upgraded from MES version 1.0 to MES version 3.0 and converted the Vision application to Perspective.
Automated Downtime Collection in Real Time
Pennsylvania
A leading manufacturer of lift equipment was dealing with extreme downtime and inefficiency on a
A leading manufacturer of lift equipment was dealing with extreme downtime and inefficiency on a paint line and was unable to point to any hard data to determine the causes. To help determine the downtime cause, MDI worked to integrate Sepasoft’s OEE Downtime module.
MDI worked with the customer to determine potential causes of downtime and developed PLC logic that when integrated with the OEE module would record any incidents causing downtime. Downtime data recorded includes cause of the downtime, when the event took place, how long the line was affected, and the number of times an event has happened. Using the data recorded, MDI created an OEE dashboard that visualizes causes of downtime and highlights incidents that caused extended periods of downtime. The data recorded is also used to send out a scheduled report indicating how much downtime there was for a particular day/shift by cause.
This resulted in the customer’s downtime visibility and tracking going from operator reported to automatically collected and displayed in real time. This allowed to customer to see trends in downtime that allowed them to better improve their manufacturing process, as well as improved accountability from their operators.
Since implementing this project, MDI has upgraded from MES version 1.0 to MES version 3.0 and converted the Vision application to Perspective.
MDI worked with the customer to determine potential causes of downtime and developed PLC logic that when integrated with the OEE module would record any incidents causing downtime. Downtime data recorded includes cause of the downtime, when the event took place, how long the line was affected, and the number of times an event has happened. Using the data recorded, MDI created an OEE dashboard that visualizes causes of downtime and highlights incidents that caused extended periods of downtime. The data recorded is also used to send out a scheduled report indicating how much downtime there was for a particular day/shift by cause.
This resulted in the customer’s downtime visibility and tracking going from operator reported to automatically collected and displayed in real time. This allowed to customer to see trends in downtime that allowed them to better improve their manufacturing process, as well as improved accountability from their operators.
Since implementing this project, MDI has upgraded from MES version 1.0 to MES version 3.0 and converted the Vision application to Perspective.
OEE and Integration with ERP
Glen Rock, PA
A leading developer and manufacturer of adhesives partnered with MDI to give them visibility into
A leading developer and manufacturer of adhesives partnered with MDI to give them visibility into their production process for two lines and integration with their ERP system. The existing process did not have any visibility of real-time production data. This made it impossible for the operations team to see areas of the process that could be improved upon. The customer seeked a fully featured MES solution that allowed for scalability to future lines and the ability to integrate track and trace features.
Key data points the client was looking for included changeover timing and duration, live production counts, and line downtime reasons. MDI collaborated with the client to determine the best approach to collect the production data from the PLC’s. We developed a set of perspective dashboards that the operations team can use to identify areas needing improvement.
MDI also utilized the Web Services module to retrieve ERP data via barcode scan. By leveraging this data (retrieved via API), we defined new materials, created work orders, scheduled production runs, and started OEE Changeover automatically. This eliminated the need for operators to manually trigger these events and avoided inaccurate time stamps.
Key data points the client was looking for included changeover timing and duration, live production counts, and line downtime reasons. MDI collaborated with the client to determine the best approach to collect the production data from the PLC’s. We developed a set of perspective dashboards that the operations team can use to identify areas needing improvement.
MDI also utilized the Web Services module to retrieve ERP data via barcode scan. By leveraging this data (retrieved via API), we defined new materials, created work orders, scheduled production runs, and started OEE Changeover automatically. This eliminated the need for operators to manually trigger these events and avoided inaccurate time stamps.
2023-03-06 - 2023-07-11
Locations
SHREWSBURY, PA
US
39 E FORREST AVE STE 12
Kevin Morabito
Allentown, PA
US
5925 Tilghman St. Suite 800
Kevin Morabito
Contact
Kevin Morabito

OEE Gold Certified
5 Engineers

OEE Certified
1 Engineer

OEE Credentialed
3 Engineers

SPC Gold Certified
3 Engineers

SPC Credentialed
3 Engineers

Settings & Changeover Gold Certified
3 Engineers

Settings & Changeover Credentialed
3 Engineers

Track & Trace Gold Certified
2 Engineers

Track & Trace Certified
1 Engineer

Track & Trace Credentialed
3 Engineers

Business Connector Certified
1 Engineer

Business Connector Credentialed
1 Engineer