Insight Engineering
Sepasoft MES Gold Integrator
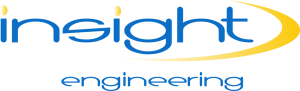
Nimble, Agile, Thorough, Flexible, Cost-efficient. Since 1992, we have been assisting our clients with best-practice Design, Programming, Systems and Support. As a Sepasoft MES Accredited - OEE and Track & Trace - Integrator, we offer end-to-end Manufacturing Operations Management systems fully integrated with existing Plant.
MES Certifications
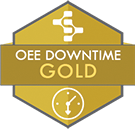
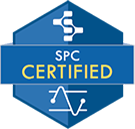
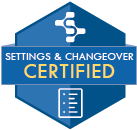
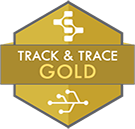
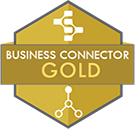
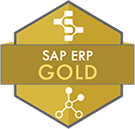
6 Gold AND 1 Credentialed MES ENGINEERS
1 LOCATIONS
Projects
OEE 2.0 Implementation for Beverage Mfr
South Australia
The Implementation of OEE on a rapid manufacturing line capable of creating over 200 parts
The Implementation of OEE on a rapid manufacturing line capable of creating over 200 parts per minute allowing them to measure their losses effectively both in terms of downtime and rejects.
Through the use of Sepasoft and Ignition the customer has achieved a thorough insight into their production capabilities. The management team holds a weekly production meeting which used to require hours of data gathering from various personnel. With the OEE package all this information is at their fingertips with ad-hoc reports.
Their operators have saved significant time in the form of automatic classification of downtime reasons compared to their old system which requires significant data entry for any and all events.
Through the use of Sepasoft and Ignition the customer has achieved a thorough insight into their production capabilities. The management team holds a weekly production meeting which used to require hours of data gathering from various personnel. With the OEE package all this information is at their fingertips with ad-hoc reports.
Their operators have saved significant time in the form of automatic classification of downtime reasons compared to their old system which requires significant data entry for any and all events.
OEE 3.0 to Replace Outdated System
Ballarat, Victoria, AU
The implementation of OEE on the clients manufacturing lines allowed them to replace a deprecated
The implementation of OEE on the clients manufacturing lines allowed them to replace a deprecated and outdated software solution providing limited feedback while simultaneously giving site personnel a more transparent view of their production.
Through the use of the Sepasoft and Ignition the customer has gained greater insights into nuisance faults occurring on their manufacturing lines, empowering them to find causes of intermittent quality issues, and to update their training around unplanned downtimes.
With the data collected via the OEE module and visualization through the Ignition Perspective platform site operators are able to effectively see downtimes as they occur live on the system, while management can see a holistic view of their manufacturing with the click of a button.
Through the use of the Sepasoft and Ignition the customer has gained greater insights into nuisance faults occurring on their manufacturing lines, empowering them to find causes of intermittent quality issues, and to update their training around unplanned downtimes.
With the data collected via the OEE module and visualization through the Ignition Perspective platform site operators are able to effectively see downtimes as they occur live on the system, while management can see a holistic view of their manufacturing with the click of a button.
2022-07-18 - 2023-06-05
T&T, OEE, and SAP Connectivity for F&B Mfr
Castlemaine, AU
The Digital Shop Floor (DSF) Project was implemented to achieve the following high-level goals:
1. Remove
The Digital Shop Floor (DSF) Project was implemented to achieve the following high-level goals:
1. Remove all paper work from their production floor including manual quality assurance data capture
2. Capture downtime for their production equipment allowing the customer to analyze and modify their production processes accordingly
3. Provide end-to-end traceability for their products to and from their SAP ERP and within the production process
In addition to achieving the above goals the project also provided the following:
1. A framework project allowing for the DSF system to be implemented swiftly into other production areas of the plant
2. A scalable environment utilizing the Web Services module to pass ERP data requests and posts from front-facing gateways to a single interface gateway
3. Management of SAP stock from within the DSF project
4. Logging of all SAP transactions to and from the DSF project
In the event the client is audited all the required information is centralized in a single system and digital format allowing for easy acquisition and packaging for the auditors as well as for internal review.
1. Remove all paper work from their production floor including manual quality assurance data capture
2. Capture downtime for their production equipment allowing the customer to analyze and modify their production processes accordingly
3. Provide end-to-end traceability for their products to and from their SAP ERP and within the production process
In addition to achieving the above goals the project also provided the following:
1. A framework project allowing for the DSF system to be implemented swiftly into other production areas of the plant
2. A scalable environment utilizing the Web Services module to pass ERP data requests and posts from front-facing gateways to a single interface gateway
3. Management of SAP stock from within the DSF project
4. Logging of all SAP transactions to and from the DSF project
In the event the client is audited all the required information is centralized in a single system and digital format allowing for easy acquisition and packaging for the auditors as well as for internal review.
Locations
Fyansford, VIC
AU
255 Hamilton Highway
Richard Loth
Contact
Richard Loth

OEE Gold Certified
3 Engineers

SPC Certified
1 Engineer

SPC Credentialed
1 Engineer

Settings & Changeover Certified
1 Engineer

Settings & Changeover Credentialed
2 Engineers

Track & Trace Gold Certified
2 Engineers

Business Connector Gold Certified
5 Engineers

Interface for SAP ERP Gold Certified
4 Engineers