CanDoIt Solutions
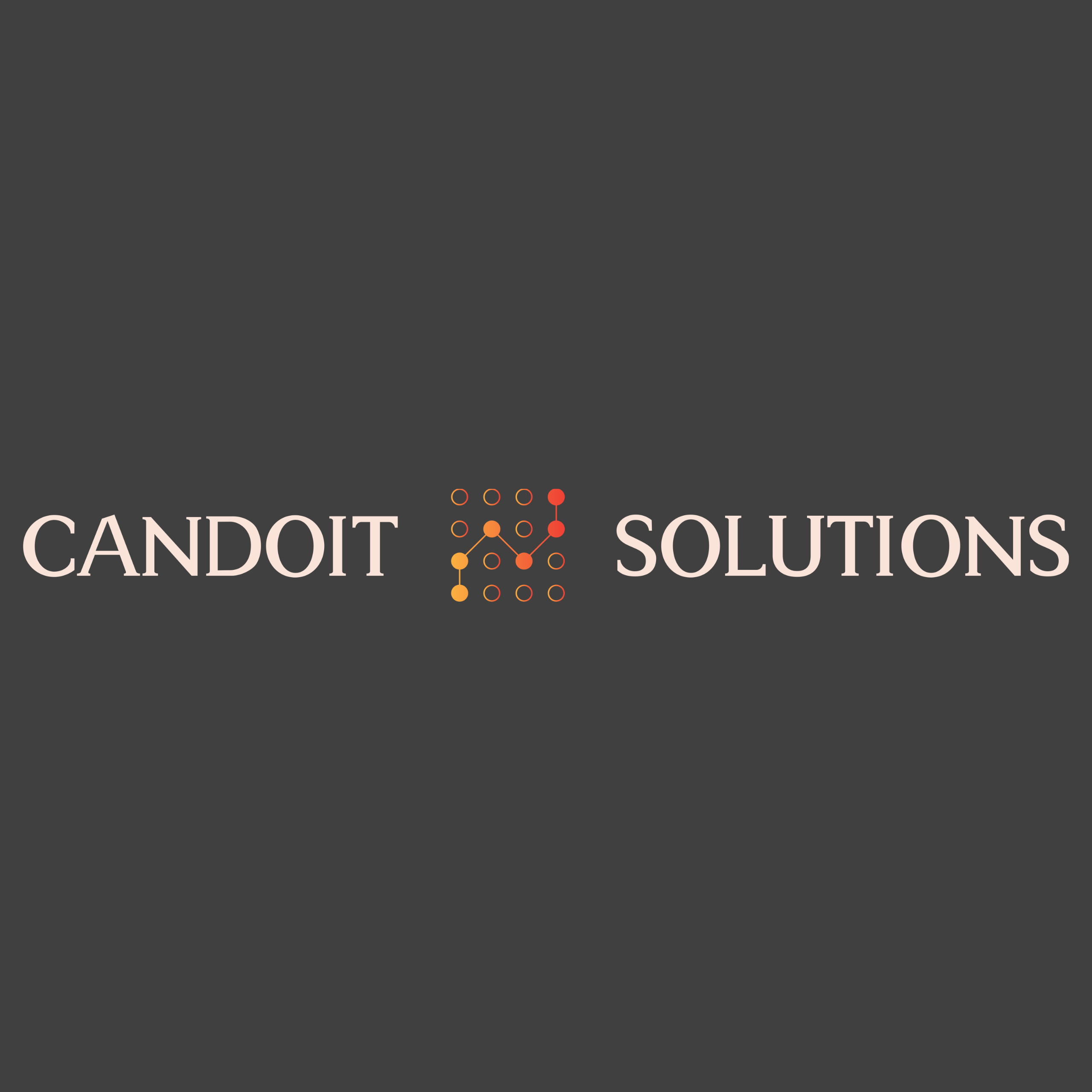
CanDoIt Solutions is a leading provider of automation and integration solutions for manufacturing and industrial facilities. With a focus on helping companies increase efficiency, reduce downtime, and improve overall performance, CanDoIt Solutions offers a wide range of services and products to meet the unique needs of each client. One of our key offerings is our expertise in Sepasoft Integrator, a powerful tool for integrating disparate systems and data sources into a unified, cohesive platform. Our team of experienced engineers and developers has deep knowledge of Sepasoft Integrator and can help businesses leverage its full potential to drive productivity and growth. In addition to Sepasoft Integrator, we offer a wide range of other automation and integration solutions, including PLC programming, SCADA development, HMI design, and custom software development. Our services are backed by decades of experience in the industry and a commitment to delivering high-quality solutions that exceed our clients\' expectations. At CanDoIt Solutions, we pride ourselves on our ability to work closely with our clients to understand their unique needs and goals. Whether it\'s optimizing a single process or overhauling an entire production line, we have the skills and expertise to deliver the solutions our clients need to succeed. Contact us today to learn more about how CanDoIt Solutions can help your business streamline operations, reduce costs, and improve overall performance.
MES Certifications
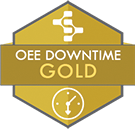
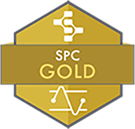
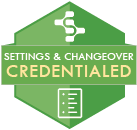
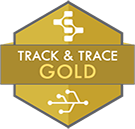
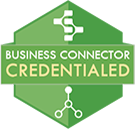
1 Gold MES ENGINEER
1 LOCATIONS
Projects
The biggest benefit from the MES implementation was the creation of a single point of truth and control for all factory operations. By leveraging Ignition and Sepasoft, PGD was able to standardize production processes and data management, ensuring material and lot traceability. This system provided real-time line performance and inventory data, allowing front-line teams to quickly address high-priority performance issues. The end-to-end connectivity from inbound materials to outbound delivery streamlined operations and opened up further opportunities for value enhancement through available data and processes.
The improvements were adopted across all departments by integrating various modules such as ERP for material codes and stock quantity control, warehouse management, dynamic production run picking, mixing, automated and manual production lines, and automated palletizing and dispatch. Each department's specific needs were addressed, leading to cohesive, efficient operations.
Cost savings were realized through increased operational efficiency, reduced manual labor, and improved inventory accuracy. By automating processes and enhancing traceability, PGD minimized waste and optimized resource usage.
Overall Equipment Effectiveness (OEE) was improved through real-time traceability and the automation of production consumption and goods issuing. Data collected included pre-start checklists, material consumption, production counts, and quality control points, which were used for performance analysis, ensuring adherence to standards, and continuous improvement initiatives. This comprehensive MES implementation has positioned PGD to better manage their complex operations and achieve sustained growth.
2023-09-01 - 2024-02-01
Locations
Contact




